Why Does Anti-reflective Coating Wear Off?
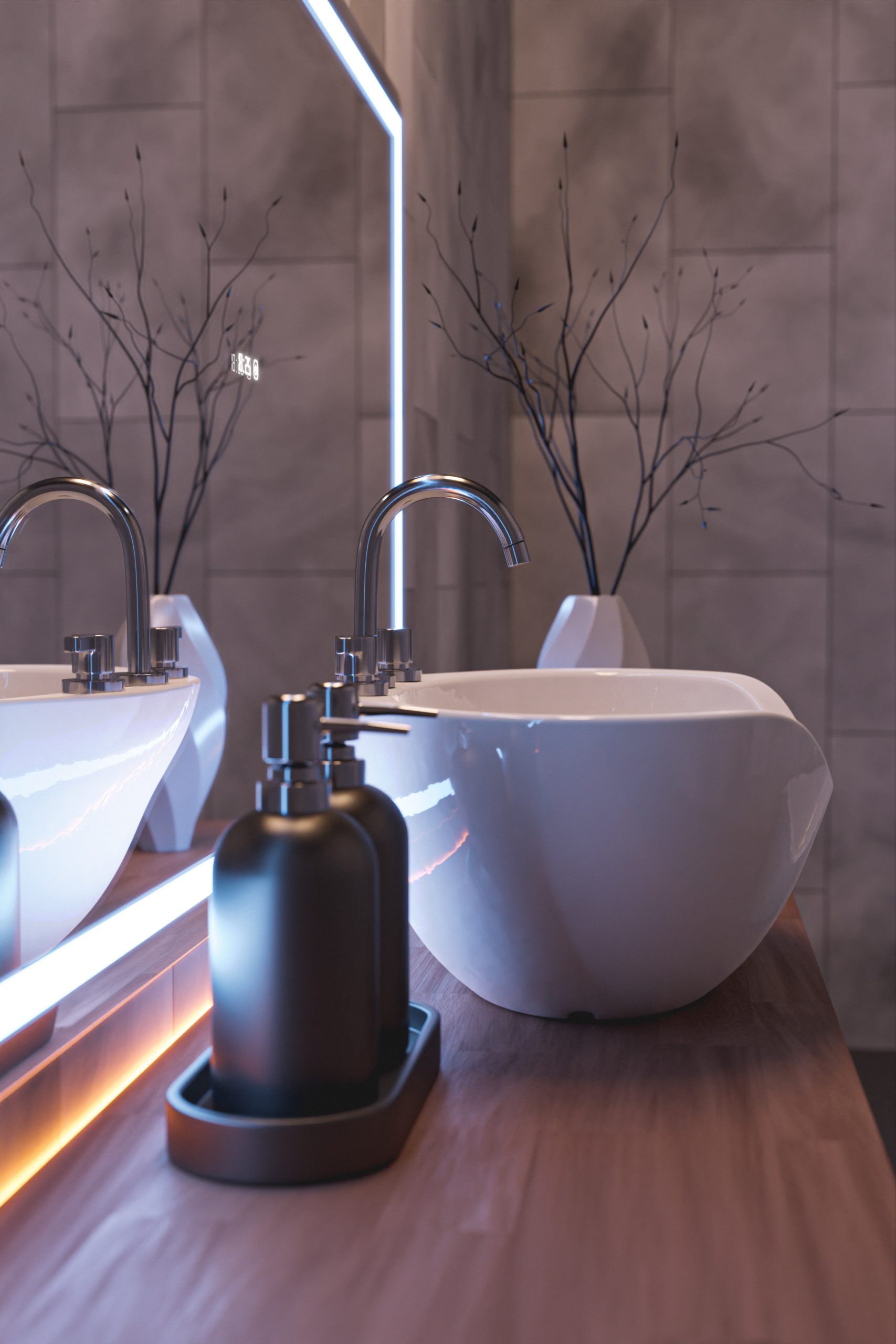
Ever wondered why the anti-reflective coating on your glasses always seems to lose its luster? It’s a frustrating experience that many of us can relate to. But have you ever stopped to wonder why this happens? In this article, I’ll uncover the reasons behind the gradual degradation of anti-reflective coating and explore the factors that contribute to its wear-off. So, let’s dig deeper into the science behind this common annoyance.
What is Anti-reflective Coating?
Definition of anti-reflective coating
Anti-reflective coating, also known as AR coating, is a thin layer of material that is applied to the surface of an optical system or device to minimize the amount of reflected light. It is designed to reduce glare, improve contrast, and enhance the overall performance of the system.
Primary function of anti-reflective coating
The primary function of anti-reflective coating is to minimize the amount of light that is reflected off the surface of an optical device, such as prescription eyeglasses, camera lenses, or smartphone screens. By reducing reflections, AR coating improves the clarity and visibility of these devices, allowing users to see more clearly and reducing eye strain.
Usual applications of anti-reflective coating
Anti-reflective coating is commonly used in a variety of applications, including eyewear, cameras, projectors, telescopes, microscopes, and precision instruments. It is also used in the automotive industry for reducing glare on windshields and side mirrors. The widespread use of AR coating is a testament to its effectiveness in improving optical performance.
How Does Anti-reflective Coating Work?
Basic concept of light reflection
When light strikes a surface, it can either be transmitted through the material, absorbed by the material, or reflected off the surface. In the case of a surface without AR coating, a significant portion of the light is reflected back, resulting in glare and reduced visibility.
Interaction of light with anti-reflective coating
Anti-reflective coating works by altering the way that light interacts with the surface it is applied to. The coating is composed of multiple layers of materials with different refractive indexes. These layers are designed to cancel out the reflections that occur at each interface, allowing more light to pass through the surface and minimizing the amount of light that is reflected off.
Role of coating’s thickness in reducing reflection
The thickness of the anti-reflective coating is carefully controlled to maximize its effectiveness. If the coating is too thin, it may not be able to sufficiently cancel out the reflections. On the other hand, if the coating is too thick, it can have a negative impact on the optical performance and may introduce unwanted optical effects. The optimal thickness of the coating depends on the specific application and the wavelengths of light that need to be minimized.
Procedure of Applying Anti-reflective Coating
Description of the application process
The application process for anti-reflective coating involves several steps. First, the surface to be coated is cleaned and prepared to ensure that there are no contaminants or imperfections that can affect the bonding of the coating. Then, the coating material is applied using a variety of techniques, such as physical vapor deposition (PVD), chemical vapor deposition (CVD), or dip coating. After the coating is applied, it is typically cured or annealed to enhance its adhesion and durability.
Materials used in the coating
The materials used in anti-reflective coating can vary depending on the specific application and desired performance characteristics. Common materials include metal oxides, such as magnesium fluoride (MgF2), silicon dioxide (SiO2), and titanium dioxide (TiO2). These materials are chosen for their ability to reduce reflections and their compatibility with the substrate material.
Types of technologies used in applying the coating
There are several different technologies that can be used to apply anti-reflective coating. Physical vapor deposition (PVD) is a popular method that involves evaporating the coating material in a vacuum chamber and depositing it onto the surface. Chemical vapor deposition (CVD) is another technique that involves reacting gases in a heated chamber to produce a thin film on the surface. Dip coating is a simpler technique where the surface is dipped into a solution containing the coating material and then withdrawn to allow it to dry.
Factors Affecting the Durability of Anti-reflective Coating
Exposure to ultraviolet light
One of the factors that can affect the durability of anti-reflective coating is exposure to ultraviolet (UV) light. UV radiation can cause the coating to degrade and lose its effectiveness over time. This is particularly true for coatings that are used in outdoor applications or devices that are exposed to sunlight for extended periods.
Chemical interactions
The chemical environment in which the anti-reflective coating is used can also influence its durability. Certain chemicals, such as solvents, acids, or alkalis, can react with the coating and degrade its performance. It is important to avoid exposing the coating to such chemicals and to clean it using gentle methods and suitable cleaning agents.
Physical damage
Physical damage, such as scratches, abrasions, or impacts, can also compromise the durability of the anti-reflective coating. Even small scratches can disrupt the smooth surface of the coating and create areas where light can be reflected. It is important to handle coated surfaces with care and to use protective measures, such as lens caps or cases, to minimize the risk of physical damage.
Why Does Anti-reflective Coating Wear Off?
Analysis of aging process
The degradation and wearing off of anti-reflective coating over time can be attributed to several factors. One of the main reasons is the aging process, where the coating materials undergo changes due to exposure to various environmental conditions. This can lead to a gradual loss of the coating’s effectiveness and performance.
Understanding wear and tear
The wear and tear on anti-reflective coating is caused by repeated use and exposure to external factors. When the coated surface comes into contact with other objects or surfaces, it can experience mechanical stress, which can lead to the thinning or wearing off of the coating. Additionally, exposure to moisture, oils, and dirt can accumulate on the surface over time, affecting the clarity and performance of the coating.
Impact of environmental factors
Environmental factors, such as temperature, humidity, and pollution, can contribute to the wearing off of anti-reflective coating. Extreme temperatures can cause the coating to expand or contract, leading to cracks or delamination. High humidity levels can promote the growth of mold or mildew, which can degrade the coating. Pollution, such as airborne particles or chemical pollutants, can also accumulate on the surface and affect the coating’s performance.
Consequences of Wearing Off Anti-reflective Coating
Impact on optical performance
When the anti-reflective coating wears off, the optical performance of the device or system can be significantly compromised. Without the coating, more light is reflected off the surface, leading to increased glare and reduced contrast. This can make it difficult to see clearly and can cause eye strain, particularly in bright or high-contrast lighting conditions.
How it affects the user experience
The wearing off of anti-reflective coating can have a negative impact on the user experience. For example, in the case of eyeglasses, the loss of coating can result in reduced visual acuity, increased discomfort, and decreased satisfaction with the eyewear. In the case of electronic devices, such as smartphones or tablets, the loss of coating can make it harder to read or view the screen, leading to a less enjoyable user experience.
Possibility of damages to the device
In addition to the impact on optical performance and user experience, the wearing off of anti-reflective coating can also increase the risk of damage to the device or system. Without the protective coating, the surface is more vulnerable to scratches, abrasions, and other forms of physical damage. This can reduce the lifespan of the device and may require expensive repairs or replacement.
Can Worn Off Anti-reflective Coating Be Restored?
Overview of the restoration process
In some cases, it is possible to restore the worn off anti-reflective coating. The restoration process typically involves removing the remaining coating from the surface and applying a new layer of anti-reflective coating. This can be done by professionals specializing in optical coatings or through DIY kits available for certain applications.
Can all coatings be restored?
However, not all anti-reflective coatings can be restored. The feasibility of restoration depends on various factors, including the type of coating, the extent of wear, and the condition of the underlying substrate. It is best to consult with a professional to determine whether restoration is possible and to ensure that the process is carried out correctly.
Cost and time required for restoration
The cost and time required for restoring worn off anti-reflective coating can vary depending on several factors. The complexity of the application, the type of coating, and the availability of restoration services can influence the cost. Similarly, the time required for restoration can range from a few hours to several days, depending on the extent of the wear and the specific restoration process used.
Ways to Prevent Anti-reflective Coating from Wearing Off
Proper handling and maintenance
One of the most effective ways to prevent anti-reflective coating from wearing off is to handle the coated surfaces with care. Avoid touching the surface with bare fingers, as the oils on the skin can degrade the coating. Clean the surface regularly using a soft microfiber cloth and gentle cleaning agents recommended for coated surfaces. Avoid using abrasive materials or harsh chemicals that can damage the coating.
Using protective covers
Using protective covers, such as lens caps, screen protectors, or cases, can help to minimize the risk of physical damage to the anti-reflective coating. These covers provide an additional layer of protection and can help to absorb the impact of bumps or scratches. Additionally, they can also protect the coating from dirt, oils, and other environmental contaminants.
Limitations of prevention methods
While proper handling and the use of protective covers can significantly reduce the risk of wear and tear, it is important to note that these prevention methods have limitations. They cannot completely eliminate the possibility of damage or degradation of the coating over time. Therefore, it is still important to be mindful of the lifespan of the coating and to consider restoration or replacement when necessary.
Comparing Anti-reflective Coating with Other Types of Coatings
Comparison based on durability
When comparing anti-reflective coating with other types of coatings, durability is an important factor to consider. Anti-reflective coatings tend to be more susceptible to wear and degradation compared to more durable coatings, such as scratch-resistant coatings or water-repellent coatings. However, the specific durability of a coating depends on various factors, including the materials used, the application method, and the environmental conditions.
Analysis based on cost
The cost of anti-reflective coating can vary depending on the specific application and the quality of the coating. Generally, anti-reflective coatings are more expensive compared to basic coatings, such as single-layer coatings or uncoated surfaces. However, the improved optical performance and user experience provided by anti-reflective coatings can justify the higher cost for many users.
User preference and feedback comparison
Another aspect to consider when comparing anti-reflective coating with other coatings is user preference and feedback. User reviews and feedback can provide valuable insights into the performance, durability, and effectiveness of different coatings. Additionally, personal preferences, such as the desired level of reflection reduction or specific application requirements, can influence the choice of coating.
Can You Reapply Anti-Reflective Coating to Glasses?
Yes, you can reapply anti-reflective coating to glasses. However, it is a delicate process that requires professional expertise. The difference between anti-reflective and anti-glare glasses lies in their functions. While anti-reflective coatings minimize reflections, anti-glare glasses focus on reducing glare caused by bright lights. Both options aim to provide clearer vision and improve the overall appearance of eyewear.
Future Developments in Anti-reflective Coating
Advancements in coating technologies
The field of anti-reflective coating is constantly evolving, with ongoing advancements in coating technologies. Researchers and manufacturers are continually developing new materials and methods to improve the performance, durability, and application process of anti-reflective coatings. These advancements may lead to coatings that are even more effective in reducing glare, enhancing optical performance, and providing longer-lasting protection.
Emerging trends in anti-reflective coatings
One emerging trend in anti-reflective coatings is the development of self-cleaning coatings. These coatings are designed to repel dirt, oils, and other contaminants, making them easier to clean and maintain. Another trend is the use of nanomaterials in anti-reflective coatings, which can provide enhanced durability and improved optical properties.
Promising research in the field of coatings
Researchers are also exploring various promising avenues in the field of coatings. For example, there is ongoing research into anti-reflective coatings that can be applied to flexible and curved surfaces, such as smartwatches or virtual reality headsets. Additionally, efforts are being made to develop coatings that are more environmentally friendly and sustainable, reducing the use of potentially harmful materials in the manufacturing process.
In conclusion, anti-reflective coating plays a crucial role in improving optical performance, reducing glare, and enhancing the user experience in various applications. Understanding the factors affecting the durability of the coating, the consequences of wearing off, and the potential for restoration can help users make informed decisions about care and maintenance. As advancements continue to drive the field forward, the future looks promising for even more effective, durable, and innovative anti-reflective coatings.